Materials
-
High Performance > 300°F
- Polyetheretherketone (PEEK)
- Polyphenylene Sulfide (PPS)
- Polyetherimide (Ultem®)
- Sulfones
-
Engineering 185°F - 300°F
- Acetal
- Nylon
- Polyesters
- Polycarbonate
- Polyphenylene Oxide (PPO)
- Polyvinylidene Fluoride (PVDF)
-
General Industrial < 185°F
- Polypropylene
- Polyethylene
- Acrylonitrile Butadiene Styrene

Certification
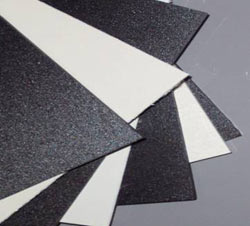
TECARAN ABS
Ensinger TECARAN™ ABS is a terpolymer and an amorphous resin. It is manufactured by combining three different compounds. The three that make up TECARAN™ ABS are acrylonitrile, butadiene, and styrene. TECARAN™ ABS occupies the unique position of being a bridge between the commodity and other higher performance engineering thermoplastics. Its performance is characterized by toughness and impact strength even at low temperatures, good stiffness and machinability.
- Cost Effective
- Good Toughness At Low Temperatures
- Easily Machinable
- Available In Natural or Black
- Meets ASTM D4673-02 ABS220B44500
- Easily Bonded
The applications for TECARAN™ ABS range from Aerospace and automotive parts and housings, to parts for agricultural lawn and garden equipment and components for medical and business equipment, as well as many others.
Properties | Condition | Value | Test Method | Comment | ||||
---|---|---|---|---|---|---|---|---|
Mechanical | Modulus of elasticity (tensile test) | @ 73°F | 270,000 | °F | ASTM D 638 | |||
Wear (K) factor | Against Steel, 40psi,50fpm | 3500*10-10 | in3-min/ft-lbs-hr | ASTM D 3702 1) | 1) Injection molded data | |||
Tensile strength at yield | @ 73°F | 5,100 | psi | ASTM D 638 | ||||
Elongation at break | @ 73°F | 15 | % | ASTM D 638 | ||||
Flexural strength | @ 73°F | 8,000 | psi | ASTM D 790 | ||||
Modulus of elasticity (flexural test) | @ 73°F | 270,000 | psi | ASTM D 790 | ||||
Impact strength (Izod) | @ 73°F | 6.3 | ft-lbs/in | ASTM D 256 | ||||
Rockwell hardness | @ 73°F R Scale | 102 | ASTM D 785 | |||||
Coefficient of friction | Static | 0.19 - 0.21 | ASTM D 3702 1) | |||||
Coefficient of friction | Dynamic, 40 psi, 50 fpm | 0.35 | ASTM D 3702 1) | |||||
Thermal | Vicat softening point |
|
224 | °F | 1) | |||
Deflection temperature | @ 66 psi | 200 | °F | ASTM D 648 1) | ||||
Deflection temperature | @ 264 psi |
177 | °F | ASTM D 648 1) | ||||
Service temperature | Intermittent | 210 | °F | - | ||||
Service temperature | Long Term |
150 | °F | 2) | 2) per UL746B | |||
Thermal expansion (CLTE) | -40F to 100F | 5.6*10-5 | in/in/°F | ASTM D 696 1) | ||||
Specific heat |
|
0.30 | BTU/lb-F° | 3) | 3) per ASTM C351, Injection molded data | |||
Thermal conductivity | 1.32 | BTU-in/hr-ft2-F° | ASTM C 696 | |||||
Electrical | Volume resistivity | 1.0*1015 | Ω*cm | ASTM D 257 1) | ||||
Dielectric strength | 450 | V/mil | ASTM D 149 1) | |||||
Dissipation factor | @ 60 Hz, 73°F | 0.02 | ASTM D 150 1) | |||||
Dielectric constant | @ 60 Hz, 73°F, 50% RH | 3.3 | ASTM D 150 1) | |||||
Other | Moisture absorption | @ 24 hours, 73°F | 0.30 | % | ASTM D 570 | |||
Moisture absorption | @ saturation, 73°F | 0.70 | % | ASTM D 570 | ||||
Flammability (UL94) | HB | 4) | 4) Injection molded data (1.5mm thick) | |||||
This information is only to assist and advise you on current technical knowledge and is given without obligation or liability. All trade and patent rights should be observed. All rights reserved. Data obtained from extruded shapes material. |