Materials
-
High Performance > 300°F
- Polyetheretherketone (PEEK)
- Polyphenylene Sulfide (PPS)
- Polyetherimide (Ultem®)
- Sulfones
-
Engineering 185°F - 300°F
- Acetal
- Nylon
- Polyesters
- Polycarbonate
- Polyphenylene Oxide (PPO)
- Polyvinylidene Fluoride (PVDF)
-
General Industrial < 185°F
- Polypropylene
- Polyethylene
- Acrylonitrile Butadiene Styrene

Certification
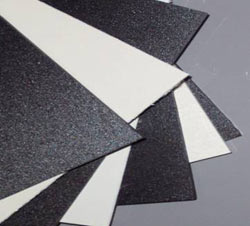
TECAFORM® AH
TECAFORM® is a semi-crystalline thermoplastic offering high strength, stiffness and toughness. TECAFORM® is resistant to hot water, hydrocarbons and solvents, and it possesses good bearing and wear properties. It is available in natural and black grades. TECAFORM® is commonly used as bushings, rollers, wear strips and other applications requiring a combination of strength, low moisture absorption, chemical resistance and dimensional stability.
- No centerline porosity
- Low moisture absorption
- Excellent machinability
- Good combination of mechanical properties
- Chemical resistance to fuels and solvents
TECAFORM™ is resistant to aqueous solutions with pH values ranging from 4 to 14. - Good wear and abrasion properties
- Good dimensional stability
- Good property retention at elevated temperatures
TECAFORM® is used in a wide variety of industrial applications requiring good strength and toughness, dimensional stability, wear resistance and the ability to operate in a wet environment with little absorption. Material handling, machinery and fluid handling are some of the common industries utilizing TECAFORM®'s combination of properties. Typical applications are gears, wear strips, bushings, pump parts, fittings and rollers.
Properties | Condition | Value | Test Method | Comment | ||||
---|---|---|---|---|---|---|---|---|
Mechanical | Modulus of elasticity (tensile test) | @ 73°F | 380,000 | psi | ASTM D 638 | |||
Tensile strength at yield | @ 73°F | 8,800 | psi | ASTM D 638 | ||||
Elongation at break | @ 73°F | 25 | % | ASTM D 638 | ||||
Flexural Strength | @ 73°F | 11,000 | psi | ASTM D 790 | ||||
Modulus of Elasticity (flexural test) | @ 73°F | 360,000 | psi | ASTM D 790 | ||||
Compression strength | 4,500 | psi | ASTM D 695 | |||||
Impact strength (Izod) | @ 73°F | 1.0 | ft-lbs/in | - | ||||
Rockwell hardness | @ 73°F M Scale | 86 | % | ASTM D 785 | ||||
Coefficient of friction | Dynamic, 40 psi, 50 fpm | .21 | ASTM D 3702 | |||||
Wear rate | 40 psi, 50 fpm | 65 x 10-10 | in3-min/ft-lbs-hr | ASTM D 3702 | ||||
Thermal | Melting temperature | 329 | °F | - | ||||
Deflection temperature | @ 66 psi | 316 | °F | ASTM D 648 | ||||
Deflection temperature | @ 264 psi | 230 | °F | ASTM D 648 | ||||
Service temperature | Intermittent | 285 | °F | - | ||||
Service temperature | Long term | 195 | °F | - 1) | 1) per UL746B | |||
Thermal expansion (CLTE) | 4.7*10-5 | in/in/°F | ASTM D 696 | |||||
Electrical | Volume resistivity | 1.0 x 1014 | Ω*cm | ASTM D 257 | ||||
Dielectric strength | 500 | V/mil | ASTM D 149 | |||||
Dissipation factor | @ 60 Hz, 73°F | 0.001 | % | ASTM D 150 | ||||
Dielectric constant | @ 60 Hz, 73°F, 50% RH | 3.7 | % | ASTM D 150 | ||||
Other | Moisture absorption | @ 24 hrs, 73°F | 0.22 | % | ASTM D 570 | |||
Moisture absorption | @ saturation, 73°F | 0.80 | % | ASTM D 570 | ||||
Flammability (UL94) | UL 94 | HB | % | 2) | 2) at 1.5mm thickness injection molded sample | |||
This information is only to assist and advise you on current technical knowledge and is given without obligation or liability. |