Materials
-
High Performance > 300°F
- Polyetheretherketone (PEEK)
- Polyphenylene Sulfide (PPS)
- Polyetherimide (Ultem®)
- Sulfones
-
Engineering 185°F - 300°F
- Acetal
- Nylon
- Polyesters
- Polycarbonate
- Polyphenylene Oxide (PPO)
- Polyvinylidene Fluoride (PVDF)
-
General Industrial < 185°F
- Polypropylene
- Polyethylene
- Acrylonitrile Butadiene Styrene

Certification
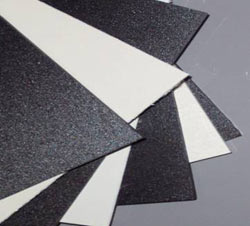
TECANYL
NORYL®, due to its inherent chemical composition, exhibits unusually low moisture absorption. Therefore, good electrical insulating properties are realized over a wide range of humidity and temperature conditions. Chemical attack from water, most salt solutions, acids and bases is also minimal with NORYL®. The addition of glass fiber reinforcement enhances both the mechanical and thermal properties of the basic NORYL® material.
- Good electrical insulating properties
Due to its extremely low water absorption with values as low as 0.07%, NORYL® is an excellent electrical insulating material. - Long-term dimensional stability
- Superior impact strength
NORYL® has a notched Izod impact strength of 3.5 ft-lbs/in. - NORYL® exhibits a continuous use temperature in excess of 220°F
- Wide range of UL flammability ratings from
UL94 HB to UL94 V-1 - Light weight
NORYL®, with a density of 0.0383 lbs/in3, can be used in applications where weight is a significant consideration. - Thermoformable capability
- Possesses good hydrolytic stability
NORYL® exhibits a broad range of outstanding properties for applications in computers and business equipment, automotive, electrical insulation, telecommunications, appliances, electronics, and many other industries.
Properties | Condition | Value | Test Method | Comment | ||||
---|---|---|---|---|---|---|---|---|
Mechanical | Modulus of elasticity (tensile test) | @ 73°F | 350,000 | psi | ASTM D 638 | |||
Tensile strength at break | @ 73°F | 9,200 | psi | ASTM D 638 | ||||
Elongation at break | @ 73°F | 25 | % | ASTM D 638 | ||||
Flexural strength | @ 73°F | 13,400 | psi | ASTM D 790 | ||||
Modulus of elasticity (flexural test) | @ 73°F | 370,000 | psi | ASTM D 790 | ||||
Impact strength (Izod) | @ 73°F | 3.5 | ft-lbs/in | ASTM D 256 | ||||
Rockwell hardness | @ 73°F R Scale | 119 | ASTM D 785 | |||||
Coefficient of friction | Static | 0.39 | ASTM D 3702 | |||||
Coefficient of friction | Dynamic, 40 psi, 50 fpm | 0.32 | ASTM D 3702 | |||||
Thermal | Vicat softening point |
|
310 | °F | - | |||
Deflection temperature | @ 66 psi | 279 | °F | ASTM D 648 | ||||
Deflection temperature | @ 264 psi |
254 | °F | ASTM D 648 1) | 1) Injection molded sample | |||
Service temperature | Intermittent | 230 | °F | - | ||||
Service temperature | Long term |
220 | °F | - | ||||
Thermal expansion (CLTE) | 3.3*105 | in/in/°F | ASTM D 696 | |||||
Electrical | Volume resistivity | @ 73°F | 1*1017 | Ω*cm | ASTM D 257 | |||
Dielectric strength | 500 | V/mil | ASTM D 149 | |||||
Dissipation factor | @ 60 Hz, 73°F | 0.0007 | ASTM D 150 2) | 2) Injection molded samples | ||||
Dielectric constant | @ 60 Hz, 73°F, 50% RH | 2.7 | ASTM D 150 | |||||
Other | Moisture absorption | @ 24 hours, 73°F | 0.07 | % | ASTM D 570 | |||
Flammability (UL94) | V-1 | 3) | 3) thickness greater than 1.5 mm, injection molded samples | |||||
Flammability (UL94) | V-0 | 4) | 4) thickness greater than 6 mm, injection molded samples | |||||
This information is only to assist and advise you on current technical knowledge and is given without obligation or liability. All trade and patent rights should be observed. All rights reserved. Data obtained from extruded shapes material. |